Integrating machines into production lines is a crucial step in optimising production, reducing costs and improving product quality.
At BENNE SA, our positioning has been clearly oriented towards automated material handling and its functionalities since 1985.
However, over the years we have gained experience in integrating machines and/or functions that we do not necessarily manufacture, but which we very frequently encounter in the automated material handling projects entrusted to us.
Optimising productivity:
Integrating machines enables repetitive processes to be automated, reducing production time, ensuring an efficient workflow, minimising downtime and smoothing the production flow, thereby increasing production capacity.
Lower costs:
Automation reduces the risk of human error, smoothes transitique flows, optimises workflows, increases production capacity and reduces lead times.
Improved quality:
Machines guarantee precision and uniformity in production, improving the quality of end products by reducing the number of faulty products and the costs of rework or correction.
Why choose us?
BENNE works with you to define a solution with the help of our sales engineers, designs it in our design offices, manufactures and assembles it in our workshops, electrifies and automates it with our specialist technicians, and then installs it in your plants with our field technicians. We can also provide maintenance for these lines.
By integrating and offering a more complete scope in the implementation of your processes, we can reduce the number of people involved and, as a result, converge more quickly and dynamically towards the objectives to be achieved.
In terms of control/command, the uniqueness of the logic improves communication between machines and between lines, to ensure the speed and precision of your product flows.
The safety of your operators is not neglected, and also benefits from a single approach covering the entire perimeter.
Our design offices guarantee global visibility of the process being worked on. No more ‘every man for himself’!
Robotics:
In recent years, we have added the integration of robots or cobots to our activities, either at the heart of the process or at the end of the line.
These tools, combined with developments in computing and electronics, are increasingly powerful and versatile, boosting productivity.
We prefer to integrate YASKAWA robots, but we can adapt to your requirements if you already have other brands in place.
They can be of any type: poly-articulated, delta, scara, AGV, cobots, etc.
They can be found within processes and at the end of the line, for palletising tasks, for example.
Here are a few examples of the machines we regularly integrate into our customers’ lines:
Stacking / destacking of pallets
Sealing (case sealers)
Strapping
Weighing and checkweighing stations
Case / carton forming
Cartoning
Flowpackaging
Pallet wrapping, hooding, corner removal
Bagging
Combined weighing
Filling
Dosing
This list is not exhaustive…
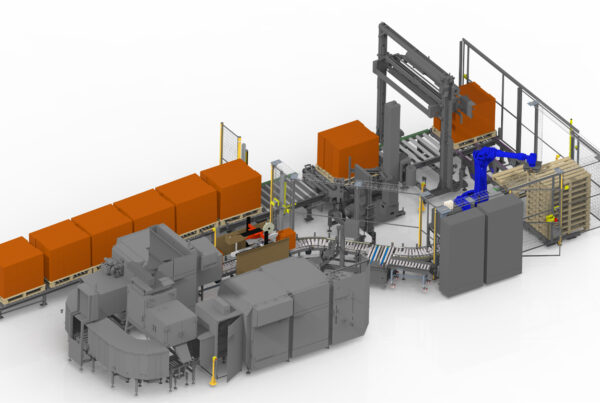
Conveyor for transporting soap pearls
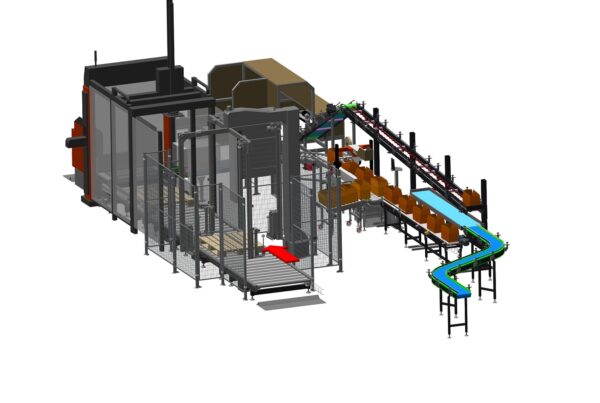
Chocolate bar packaging
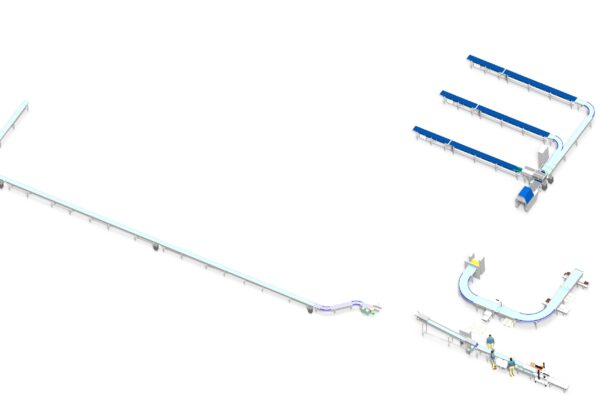
Packaging line for baked goods
OUR PROJECT PROCESS
Chronology of your projects
